It is no secret that exposed to both environmental risks and events (rain, ice, hail, snow, lightning…), blades are amongst the most at-risk components of a wind turbine. However, here at Greensolver we have often seen cases where blades are not considered by asset owners & managers as a major component impacting performance and profitability of the wind asset.
This article aims to demonstrate that Maintenance Supply Agreements do not cover all blade related risks, having direct impact on profitability and performance of a turbine, finally demonstrating the importance of having a thorough blade management system, through which savings can be made.
1. Not covered risks
Even being full-scope, MSA do not cover blade related risks. Indeed, most of them only cover important blade damage which in turn is often excluded from the availability warranty or worse, if insurance is called in, has a steep deductible franchise.
- Cosmetic damages: many contracts do not carry the obligation for the contractor to perform cleaning, resurfacing and/or painting of external parts, including blades; having a direct impact on the blade’s aerodynamic.
- Major events: most MSA exclude lightning strikes from their guarantee and yet, they are amongst the most important failures that can occur.
- Wear & tear events: minor peeling, air pockets and crack formations on the surface of the blades. They account for about 60% of damages claimed. Most turbine manufacturers won’t be held responsible if those events occur, as in most cases it isn’t a structural default and not an emergency.
- Inspection method: determining the blade state, inspection can be achieved in different ways. However, currently, only a detailed inspection with a panoramic ground HD camera or HD drone is able to determine the real blade condition. Looking closer at MSA contracts, inspection method is not guaranteed or even worse, not mentioned in the contract.
- Mean Time To Repair: MSA do not commit themselves on time they have to repair. When it comes to blades, one of the largest component of a wind turbine, replacement cannot be done as easily as with smaller parts. Indeed, whether structural or cosmetic, cranes have to be implemented to repair the damaged blade and because of that Mean Time To Repair can often vary from one day to several months.
2. Consequences on profitability & performance
Performance
Each risk identified above will have direct impact on the asset performance. Blade performance can also be impacted by other factors:
Small problems can grow into larger ones: small defaults, are often not taken seriously, though they can lead to a loss of production of about 1%. Moreover, not handled in time, small defaults can rapidly become a bigger issue, not measurable and difficult to handle leading, in the worst cases, to a complete blade failure.
Acoustic risks: often forgotten or minimized, a delaminated blade will create a whistling noise which can disturb landowners close by, raising the risk of acoustic litigation, having a direct impact on performance, especially in countries where regulation is more likely to be strict with wind farm infrastructure.
Aerodynamics: being damaged, aerodynamic profile of the blade will be modified resulting in the blade slowing down and having a direct impact on the turbine’s performance.
Chain reaction: aerodynamic of the blade being modified, consequences on other components cannot be neglected, especially on the rotor being unbalanced and vibrating more than it should. Those unexpected vibrations will have a negative impact on:
- Main bearing
- Wind turbine tower
- Gear box & main shaft
- Blade gudgeons
Profitability
If performance is impacted, profitability of the asset will be as well. Indeed, the longer the turbine is stopped, the less it produces and the less it is profitable. Moreover, production losses are not fully covered by the availability formula, meaning that even if the Maintenance Supply Agreement guarantees availability, what is lost will never be reimbursed either by the maintenance supplier or the insurance.
Production losses also have an impact on debt as it is not reimbursed as fast as it should be, insurance needing time to review the situation. From our experience, it usually take 6 months to a year to reimburse lost revenues.
In some cases, the DSRA account will be used or addiional equity funds will have to be injected in the farm, thus having direct consequences on cash management.
3. Example
French wind farm of 10 MW – 5 Repower MM82 turbines
We have recently seen a case where a blade was suffering from a delamination – not identified through regular inspection method included in MSA contracts, causing the blade to make a whistling noise.
Closed-by landowners sued the farm in justice for acoustic prejudice. The wind farm had to be shut down for 3 months and had to pay interests to landowners.
Consequences:
- Production loss: 8279,297 kWh
- Financial loss: 83,270€ – interests not included
4. Solution
Risk identification and thorough blade management are crucial to avoid performance and profitability losses. Greensolver’s team of experts have developed a program, Bladesolver, designed specifically to detect risk areas and improve blade performance.
Starting with a risk assessment audit and risk categorization report, Bladesolver aim to detect potential pitfalls of wind assets. Once risks are identified, we provide mitigation technical solutions to be implemented. Working with many suppliers of the wind sector allows us to have a large benchmark of technical solutions, amongst which:
- Detailed blade inspection
- Thunder detector
- Erosion Protection Tape
- Vortex generator
- …
We monitor blade activities through the whole duration of the contract and provide a risk categorization report updated on a yearly basis. Above all, we identify performance improvements opportunities and new technologies available to enhance asset profitablity and asset performance.
Discover Bladesolver in detail
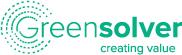