The global wind industry has endured several fatalities. Incorrect use of Personal Protective Equipment (PPE) has been indicated as the root cause to many of these incidents. At Greensolver we believe that a good Health and Safety culture is an important part of business. By writing these Safety flashes we would like to raise awareness about what is happening in the global wind Industry and share the Greensolver view on HSE.
Recent events in the Industry
The 14th of December 2016, a fatality occurred in a North-west Brazil facility; according to the Health and Safety investigators the root cause was incorrect use of PPE. On the 5th of October 2016, in Borne Germany, a worker fell through the tower section of a turbine. This accident could have been prevented if PPE was used correctly and as prescribed.
The industry has suffered more than the previously mentioned incidents where people lost their lives where the root cause can be traced back to the incorrect use of PPE. The fatalities are just the top of the proverbial iceberg. Many Lost Time Incidents, first aid treatments and near misses are caused by not using or wrongful use of the correct PPE; and this whilst the industry aims to be safe industry for every person working in it. Of course, not using, or incorrect use of PPE is not the only contributing factor responsible for incidents, accidents, injuries and fatalities, nevertheless Greensolver wants to highlight the importance of correct use of PPE.
Hazard & risk description
For anyone working in the wind energy industry, it is mandatory to wear PPE at indicated areas. PPE is protective clothing and equipment for specified circumstances or areas, where the nature of the work or conditions under which people are working, require the wearing of, or use of, personal protection to further minimize the risk of personal injuries.
With respect to PPE, the following hazards are identified: selection of the wrong PPE for the task and its associated risks, failure to use PPE, wrong or improper use of PPE and bad or no maintenance of PPE. These hazards can lead to the risks that staff is insufficiently protected, incidents and accidents resulting in injuries or fatalities and liabilities due to noncompliance to local and international laws and regulations.
Greensolver advice
Greensolver advises to always carry out risk assessments. Always follow the As Low As Reasonably Practicable (ALARP) principle. When risk can be avoided: avoid. If the risk can’t be avoided mitigate risks at the source by design. If that is not possible put in place safe guards, after placing this the next mitigations should be awareness devices and signs. If there is still a residual risk the owner/employee has to make sure the correct procedures and training are in place to further reduce risk. When all this is done the last residual risk that still remains needs to be mitigated by PPE. Greensolver advises the following for respectively companies and employees:
As company:
- Carry out risk assessments;
- Inform your employees about the risks in your workplace;
- Provide the correct PPE for the job;
- Select PPE which are CE marked;
- Ensure all PPE is certified by an approved company and have them checked every year;
- Provide training where needed on the safe use of PPE;
- Inform your staff about the importance of correct PPE use;
- Ensure PPE is stored correctly when not in use;
- Appoint who is responsible for the acquiring and maintenance of PPE.
As employee:
- Always carry out pre-use PPE inspections;
- Always carry out a last-minute risk assessment to see if you have the correct PPE for the task.Use your PPE according to use instructions and procedures;
- Always use the correct PPE at the indicated area’s;
- Always report damages of your PPE to the responsible person;
- Take care of your colleagues, when you see something is wrong with their PPE;
- If you have any questions about the use of PPE contact your HSE Manager.
If you are unsure that the measures you have in place are sufficient, do not hesitate to contact us!
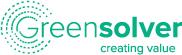